
dans l'industrie de la construction
Le système robotique issu des travaux des chercheurs de l’université du Maryland et du NICTA, un centre de recherche d’informations et de technologie informatique en Australie, est capable d’apprendre des processus en regardant des vidéos sur YouTube. Dans un billet blog, les chercheurs expliquent que « notre but ultime est de concevoir un robot autodidacte en mesure d’enrichir ses connaissances sur la manipulation de fines graines en regardant des vidéos de démonstration ». Le robot se sert de la reconnaissance d’objets et de types en parallèle à un framework d’apprentissage qui lui permet de compiler une banque croissante de compétences et de fonctions. Il peut reconnaître ce qu’une personne tient dans une vidéo, apprend comment elle le tient, et convertit ses actions en étapes reproductibles ».
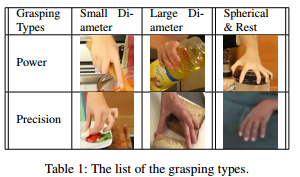
Il n’est pas difficile de voir comment de tels systèmes pourraient être utilisés pour améliorer la fabrication automatisée ou apporter de nouveaux systèmes d'automatisation pour les zones de production qui n’en bénéficient pas encore largement. Un investissement dans un système robotique unique capable d'apprendre une variété de tâches sans programmation spécialisée serait attrayant pour les petits fabricants qui font des cycles de production courts, par exemple. Un robot qui peut apprendre en regardant les autres pourrait également affiner ses propres actions par les essais et les erreurs, puis apprendre essentiellement de ses erreurs. Voilà ce que des chercheurs de l'Université de Technologie de Lappeenranta (UTL) en Finlande avaient à l'esprit quand ils ont développé un système d’auto-ajustement de soudage. Le système utilise des capteurs commandés par un programme de réseau neuronal pour détecter des erreurs dans le processus de soudage et de calculer d'autres erreurs qui sont susceptibles de survenir. Il corrige ses propres erreurs tout en apprenant à éviter de futurs dérapages. En effet, le système devient meilleur et plus efficace de lui-même, sans avoir besoin de l'intervention et de l'optimisation d'un technicien.
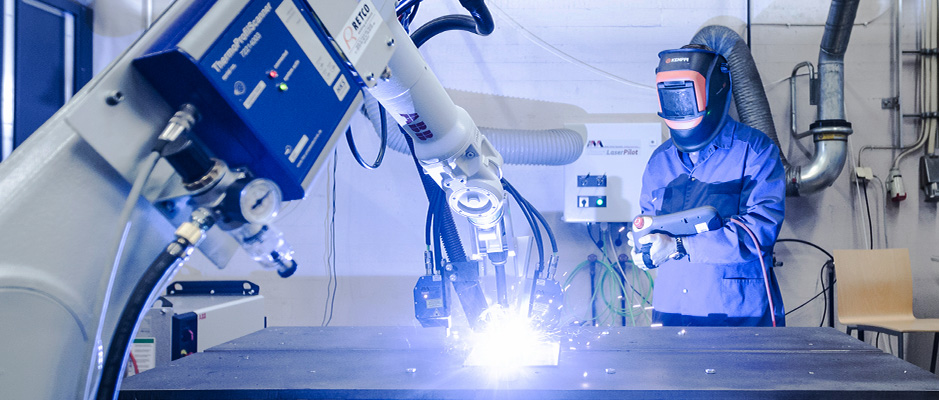
soudeur autodidacte de l'UTL
Le système développé par UTL a été spécifiquement conçu pour le soudage d’acier à haute résistance, un matériau utilisé dans des conditions extrêmes qui peut s’avérer difficile à manipuler. « Dans l’Arctique, les soudures doivent être de meilleure qualité que dans les régions chaudes », a expliqué le gestionnaire produit Markku Pirinen. « Dans le Nord, des erreurs auraient des conséquences catastrophiques. Par exemple les soudures doivent être capables de résister à des températures allant jusqu’à -60 ° C et ne doivent pas présenter de failles ». Pirinen a indiqué que le système intelligent de soudage fera réaliser d’importantes économies en éliminant le besoin de contrôles et les réparations post-soudage.
Le potentiel pour des systèmes de fabrication entièrement automatisés et autodidactes ont conduit à la mise en place d’un consortium d'entreprises et d'institutions dirigées par l'Université de Nottingham à lancer le projet Fast Ramp-Up and Adaptive Manufacturing Environment (FRAME – Montée rapide et adaptative des environnements de construction - ) il y a déjà quelques années. « L'objectif du projet FRAME est un changement de paradigme du système humain conventionnel de montée en puissance et des processus des systèmes d’intégration en des systèmes de productions automatisés et autodidactes » a indiqué le rapport présentant FRAME. Une montée en puissance est nécessaire chaque fois qu’un dispositif de fabrication est déplacé, déployé ou construit et implique généralement un processus intensif de peaufinage et d’optimisation. Il arrive que les techniciens fassent des essais pour obtenir un rendement maximal des dispositifs et cela peut finir par coûter un temps d’arrêt significatif dans la fabrication étant donné qu’il peut y avoir des erreurs.
FRAME s’intéresse aux dispositifs médicaux, des industries de l’automobile ou de l’aérospatiale qui représentent des défis et des contraintes uniques dans l’industrie de la fabrication. Le projet espère développer un système pour réduire le temps d’accès au marché de 30% pour les machines nouvellement configurées. Les chercheurs ont tenté de le faire en créant des systèmes qui ont d’abord appris des humains. En corrélant les actions des opérateurs à l’évolution de la productivité, le système FRAME pourrait commencer à résoudre des problèmes sans qu’une intervention humaine ne soit nécessaire. A l’image de la machine de soudage de l’UTL, le système serait capable de détecter les erreurs et prendre les mesures nécessaires de lui-même pour les corriger.
Durant la période d’essai, le projet FRAME a montré un taux d’échec 30% plus faible, un accroissement des sorties idéales de 64% et une amélioration dans le cycle de production de 12%. Les chercheurs veulent donc désormais adapter FRAME aux industries.
Source : LUT, UMIACS, FRAME
Et vous ?

Vous avez lu gratuitement 1 418 articles depuis plus d'un an.
Soutenez le club developpez.com en souscrivant un abonnement pour que nous puissions continuer à vous proposer des publications.
Soutenez le club developpez.com en souscrivant un abonnement pour que nous puissions continuer à vous proposer des publications.